GUIDED BY INNOVATION
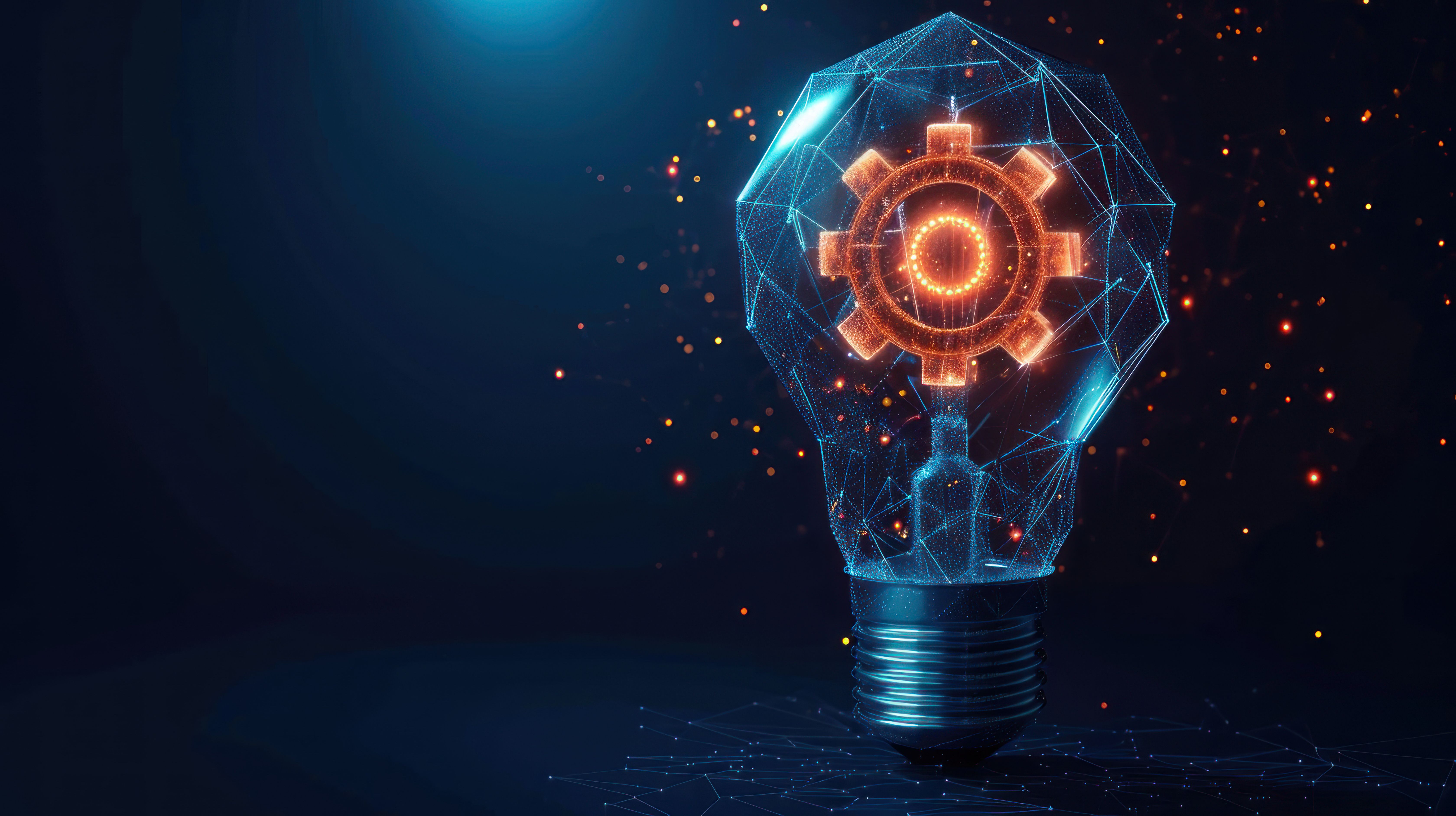
Flexible processes for compounding
Quality, sustainability and modern technology are the cornerstones of what we do!
Innovation and continuous improvement are among our core principles / Innovation and continuous improvement are at the heart of our corporate philosophy. We minimize waste in all processes through targeted efficiency improvement initiatives that benefit both PolyComp and our customers. As sustainability is our top priority, we have implemented measures to reduce energy consumption in our processes and facilities.
We create added value in our customers' supply and production chains through efficient solutions. We work with suppliers and partners who pursue the same goals. In order to continuously improve methods and processes, PolyComp has implemented quality and energy standards and initiatives that we are committed to pursuing. Your advantage: You have a long-term, reliable partner with unsurpassed industry expertise at your side who consistently focuses on quality and sustainability..
We provide modern technology
We use computer-controlled mixing and dosing systems, extruder systems and conveyor systems to process plastics. The extruders are fed both in a controlled batch process and via continuous differential feeders. To ensure maximum process flexibility, we have installed extrusion technologies from Berstorff, Coperion Buss and FEDDEM. The high-speed, high-torque single-screw and twin-screw extruders provide optimum conditions for processing at high and low temperatures - and the necessary control for shear or temperature-sensitive materials.
To meet all customer requirements in terms of handling, dosing and processing, pelletizing is carried out as strand or underwater pelletizing. Our process experience covers a wide range of polymers - e.g. PP, PE, PLA, PBAT, PHA, PA, PBT and PET. The plastics can also be modified with fillers such as talc, glass reinforcements and elastomers for higher impact strength or blended with various additives and pigments to obtain colored compounds.
How can we help you?
Would you like to find out more about our expertise? Contact one of our specialists.
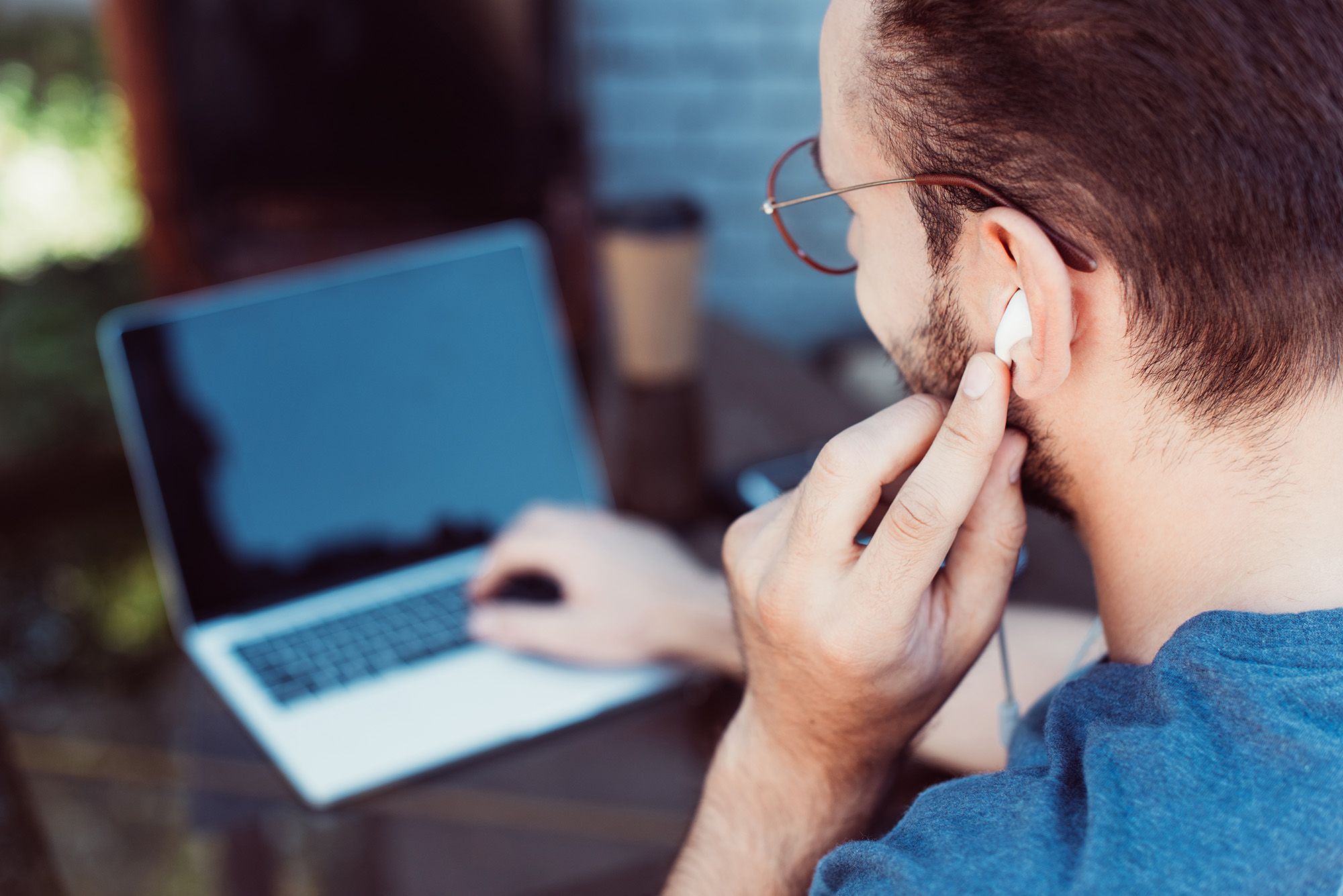